What is PEM electrolyzer?
(1) The PEM water electrolyzer adopts proton exchange membrane to isolate the gas on both sides of the electrode, avoiding the disadvantage that the gas of alkaline electrolytic hydrogen production diaphragm is easy to penetrate.
(2) The equipment mainly contains PEM electrolyzer and BOP.

What is PEMWE?
The PEM water electrolyzer uses solid proton exchange membrane PEM as the electrolyte and pure water as the reactant. Due to the low hydrogen permeability of the PEM electrolyte, the generated hydrogen is of high purity and only water vapor needs to be removed, making the process simple and safe; the electrolyzer adopts a zero-pitch structure with low ohmic resistance, significantly improving the overall efficiency of the electrolysis process and being more compact; the pressure regulation range is large and the hydrogen output pressure can reach several megapascals, adapting to the rapidly changing renewable energy power input.
1.PEM electrolyzer principle
While the main structure of the electrolyzer is similar to that of a fuel cell stack, divided into membrane electrodes, pole plates and gas diffusion layers.
Then the anode of the PEM electrolyzer is in a strongly acidic environment (pH ≈ 2) and the electrolytic voltage is 1.4~2.0 V. Most non-precious metals corrode and may bind to the sulfonic acid ions in the PEM, which in turn reduces the ability of the PEM to conduct protons.

2.Catalyst
The electrocatalysts studied in PEM electrolytic baths are mainly noble metals/oxides such as Ir, Ru and their binary and ternary alloys/mixed oxides, with titanium materials as the carrier for the loaded catalysts. And the current anodic iridium catalysts have a loading in the order of 1 mg/cm2 and the cathodic Pt/C catalysts have a Pt loading of about 0.4~0.6 mg/cm2. The Ir0.7Ru0.3Ox catalyst prepared by the Italian research team achieved an electrolytic cell performance of 3.2 [email protected] V at a total anode catalyst loading of 1.5 mg/cm2. But the full cell performance reached 2 [email protected] at an Ir loading of 1/5 of the conventional electrode. The total loading of Pt catalyst on the membrane electrode should be reduced to 0.125 mg/cm2.
The electrocatalytic oxygen precipitation activity of Ru is higher than that of Ir, but the stability is poor; the activity and stability of the catalyst can be improved by forming a stable alloy with Ir. And the Ir0.6Sn0.4 catalyst prepared by the Dalian Institute of Chemical Physics, Chinese Academy of Sciences, showed a performance of 2 [email protected] V in a full electrolytic cell test; IrSn can form a stable solid solution structure, and the process of forming an alloy with Sn improves the dispersion of Ir and helps to reduce the Ir loading.
The National Renewable Energy Laboratory (NREL) and Giner Corporation have collaborated to develop a variety of metal organic framework (MOF) material catalysts at 1/20th the price of conventional catalysts, including the Co-MOFG-O catalyst with an overpotential of 1.644 V at 0.01 A/cm2 (vs. RHE), which outperforms conventional Ir catalysts in half-cell decay experiments but has not yet been tested. full-cell tests have not been performed.

3.Gas diffusion layer



4.PEM and membrane electrodes
PEM membranes include DuPont’s Nafion series, Dow’s Dow series, Asahi Glass’s Flemion series, Asahi Kasei’s Aciplex-S series, Tokuyama Chemical’s Neosepta-F, etc. Giner’s DSMTM membranes have been produced on a large scale and have better mechanical properties, thinner thickness and better dimensional stability during power fluctuations and startup/shutdown than Nafion membranes. ‘
The DSMTM membrane developed by Giner has been produced on a large scale and has better mechanical properties, thinner thickness and better dimensional stability during power fluctuation and start-up and shutdown than Nafion membrane, and has better performance in actual electrolytic cell applications. Domestic PEM products are in the trial stage.
The anode for PEM water electrolysis needs to be resistant to acidic environmental corrosion, high potential corrosion, and should have a suitable pore structure for gas and water to pass through. Due to the reaction conditions of PEM water electrolysis, the membrane electrode materials (e.g. carbon materials) commonly used in PEM fuel cells cannot be used for water electrolysis anodes.
While 3M has developed nanostructured thin film (NSTF) electrodes with Ir and Pt catalysts at 0.25 mg/cm2 for both cathode and anode respectively; A你they can work stably under acidic environment and high potential conditions, and the rod-like array structure on the surface facilitates the surface dispersion of catalysts. But Proton used direct spray deposition to reduce catalyst agglomeration by depositing Pt/C and Ir at 0.1 mg/cm2 and IrO2 at 0.1 mg/cm2 on Nafion117 films; the performance of the single cell was similar to that of conventional high catalyst loading cells (1.8 A-cm-2@2 V). -2@2 V), with a stable operation at 2.3 V for 500 h.

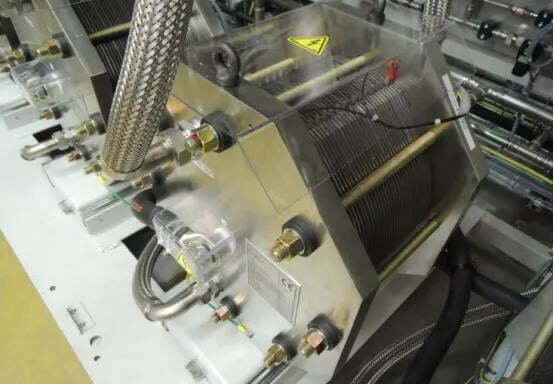
Part | Assumptions | Notes |
Membrane | Nafion 117 (purchased part) | Alternatives include PFSA (PEEK,PB) memvranes |
Pt | Pt-price=1,500/tr.oz | U.S Department of Energy (DOE) current value |
CCM | Platinum loading: Anode:7 g/m² Cathode:4 g/m² (Pt-lr) | Spray coating (altemative processed include slot-die coating and screen printing) |
PTL | Sintered porous titanium (anode side) Caron paper (cathode side) Titanium power price=$35/kg | Ti-PTL Porosity=30%; Ti-PTL coated with gold (100 nm) Carbon cloth: Toray Paper 090- TGP-H-090 (thickness=280um) |
Frame | PPS-40GF or PEEK thermoplastics | 0.625 cm from each side of the CCM was used for MEA frame bonding (injection molding) |
Plates | Stamped stainless steel 316L sheets Thickness=5 mm | Coated with gold (100nm) |
5.Equipment parameters
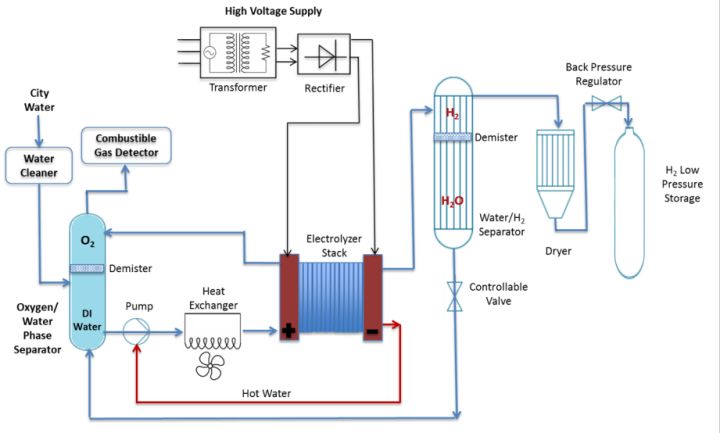
Parameter | Value | |
Stack | 200 Kw | 1000 Kw |
Gross system power | 220 Kw | 1100 Kw |
Average hydrogen H2 | 30 Nm³/hr | 170 Nm³/hr |
Average H2 production rate | 80 kg/day | 400 kg/day |
Turndown ratio | 0%-100% | 0%-100% |
Operating Pressure | 0-30 bar | |
Toatl plate area | 957 cm² | |
CCM coated area | 748 cm² | |
Single cell active area | 680 cm² | |
Gross cell inactive area | 9 % | |
Single cell amps | 1156 A | |
Current density | 1.70 A/cm² | |
Reference voltage | 1.70 V | |
Power density | 2.89 W/cm² |
The bipolar plate accounts for about 48% of the cost of the electrolyzer, and the membrane electrode accounts for about 10%. And the current international advanced level of PEM is: single cell performance of 2 A-cm-2@2 V, total platinum catalyst loading of 2~3 mg/cm2, stable operation time of 6×104 ~8×104 h, and hydrogen production cost of about US$3.7 per kg of hydrogen. And the research to reduce the cost of PEM electrolyzer is focused on the core components such as the catalyst, membrane electrode with PEM as the base material, gas diffusion layer, and bipolar plate.

