The process of making Titanium Fiber Felt for PEM usually includes the following major steps:
Raw Material Selection:
High quality titanium sponge or other titanium alloys are selected as raw materials to ensure the performance of the final product.
Titanium Crystal Preparation:
Raw materials are treated to make titanium crystals according to the metal content requirements of Titanium Fiber Felt for PEM. This process may include chemical treatments, high temperature treatments, etc.
Forging and forming:
Forging the titanium crystals into the desired shape to ensure that they have the proper physical properties.
Titanium fibre processing:
Processing titanium sheet into micron-sized titanium fibres, either mechanically or chemically. This step is critical to making Titanium Fiber Felt for PEM and affects the pore structure and strength of the final product.
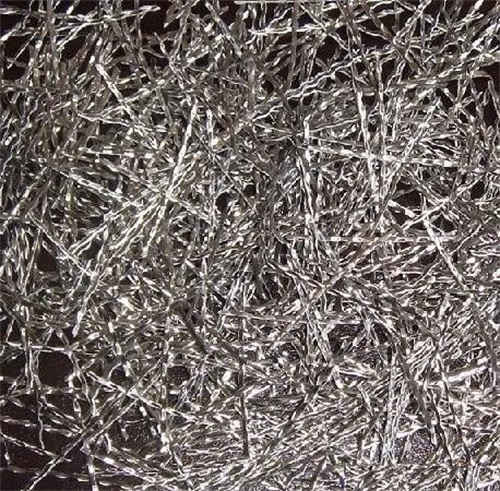
Laying of Titanium Fibres:
The processed titanium fibres are laid down to form a three-dimensional mesh. The lay-up can be done manually or using automated equipment.
High temperature sintering:
The laid titanium fibres are sintered in a high temperature vacuum furnace. This process removes excess gases and impurities and creates connections between the fibres to form a stable porous Titanium Fiber Felt for PEM structure.
Post-treatment:
After sintering, post-treatments, such as surface treatment or fine processing, may be required to improve the performance and suitability of the Titanium Fiber Felt for PEM.
Quality Inspection:
Finally, the manufactured Titanium Fiber Felt for PEM is subjected to rigorous quality testing to ensure that it meets specific technical specifications and application requirements.
Through the above steps, high-performance Titanium Fiber Felt for PEM can be produced to meet the needs of water electrolysis hydrogen production.