A water electrolysis hydrogen production system (PEM water electrolyser or alkaline water electrolyser) generally consists of a variety of key accessories, each component playing a specific role in the hydrogen production process. The following are common water electrolysis hydrogen production system accessories:
- Electrolyser
Electrolyser body: Contains the cathode and anode, which are used for the decomposition of water to produce hydrogen and oxygen.
Electrode materials: including anode (oxygen side) and cathode (hydrogen side), usually made of precious metals (e.g. platinum, iridium) or nickel-based alloys to provide excellent electrocatalytic performance.
Proton Exchange Membrane (PEM) or Diaphragm: In a PEM electrolyser, a proton exchange membrane separates the cathode from the anode and allows protons to pass through. In alkaline electrolysers, a porous diaphragm is used to separate the gases and prevent mixing of the electrolyte.
- Gas Diffusion Layer (GDL)
Titanium fibre mats or mesh (PEM electrolyser) or carbon paper (alkaline electrolyser): GDLs are used to uniformly distribute the reaction gases, to discharge the generated hydrogen and oxygen, and to enhance the efficiency of gas-liquid mass transfer. Titanium fibre mats with high porosity and excellent electrical conductivity are suitable for long-term use under high voltage conditions.
- Bipolar plate (Bipolar Plate)
Usually made of titanium, nickel alloy or graphite, the bipolar plate in the electrolytic cell to play a conductive and conductive role to support the reaction. Titanium bipolar plates are used in PEM electrolysers, while graphite bipolar plates are more commonly used in alkaline electrolysers.
- Flow field plate
Flow field design: Designs such as parallel flow field, serpentine flow field, etc. are used to distribute water and gases and to control flow paths for uniform distribution of reactants and discharge of generated gases. Usually the flow field structure is machined on the surface of bipolar or unipolar plates.
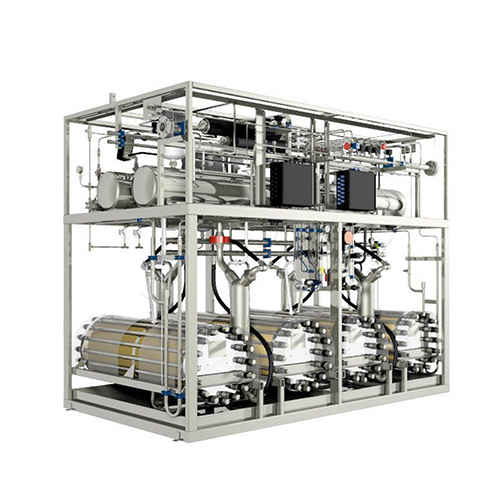
- Catalyst
Anode catalyst: usually iridium oxide, iridium black, etc., responsible for the oxidation of water to oxygen. Iridium-based catalysts are highly resistant to corrosion and are suitable for working in acidic environments.
Cathode catalyst: e.g. platinum or platinum-based alloy catalyst, used to reduce protons on the cathode side to generate hydrogen. The catalyst is loaded on the electrode or GDL to provide efficient reaction activity.
- Sealing materials
Sealing gaskets or O-rings: Seal the components inside the electrolyser to prevent electrolyte leakage and gas mixing. They are usually made of corrosion-resistant and high-temperature-resistant materials (e.g. PTFE, Viton) to ensure the sealing of the electrolyser.
- Electrolyte
In alkaline water electrolysers, potassium hydroxide (KOH) or sodium hydroxide (NaOH) solutions are often used as the electrolyte, while PEM electrolysers rely on proton exchange membranes to conduct protons, and therefore do not require an electrolyte.
- Control systems
Power control: The electrolyser is usually powered by a regulated power supply that controls the current, voltage and reaction temperature.
Temperature and pressure control: The efficiency and safety of the water electrolysis process is closely related to temperature and pressure, which the control system regulates in real time through sensors and controllers.
Gas Flow Meters and Pressure Sensors: The flow and pressure of hydrogen and oxygen are monitored to ensure safe and efficient operation.
- Cooling system
Cooling channels: Cooling waterways or heat sinks are installed inside the electrolyser to avoid the heat generated during the electrolysis process from affecting the performance and safety of the equipment.
Cooling fan or coolant: In high power electrolysis unit, external air or liquid cooling system can be added to keep the operation temperature stable.
- Water treatment system
In order to avoid the accumulation of impurities and catalyst poisoning in the electrolysis tank, usually equipped with deionised water or ultra-pure water supply system to ensure that the water entering the electrolysis tank meets the required purity.
- Gas treatment system
Gas Separator: Separate the hydrogen and oxygen generated to prevent the gas mixture from causing safety problems.
Dryer: removes water from hydrogen and oxygen to ensure that the purity of the gas meets downstream use standards.
Gas storage system: stores and distributes the generated hydrogen to provide a stable supply of hydrogen.
- Monitoring and protection devices
Sensors and Alarms: Hydrogen and oxygen are flammable and explosive gases. Electrolysers are usually equipped with gas detection sensors, temperature sensors and pressure alarms to ensure safe and stable operation of the system.
Automatic control and data logging system: This includes a PLC or DCS system, which is responsible for monitoring and regulating the operating parameters, as well as historical data logging for optimisation and maintenance.
Each component plays a different key role in the process of hydrogen production by water electrolysis, ensuring an efficient, safe and durable electrolysis process. A combination of high-performance materials and sophisticated technology is the key to achieving stable operation of a water electrolysis hydrogen plant.