Titanium Fiber Felt for PEM production technology involves the requirements of high precision, high purity and high stability, and is a technically difficult process. The following are the main technical difficulties and requirements in the production of Titanium Fiber Felt for PEM:
- Preparation of high purity titanium fibre
Technical difficulties: Titanium fibre is the core raw material of Titanium Fiber Felt for PEM, and its purity and performance directly affect the quality of the final product. The preparation of titanium fibre needs to ensure:
High purity (usually ≥99.6%).
Uniform structure free of impurities and defects
Good mechanical properties such as strength and toughness.
Solution:
Use vacuum melting process to purify titanium material and produce fibres by high precision equipment to ensure consistency and uniformity of fibres.
- Precision control of micron-sized fibre lay-ups
Technical difficulties:
Titanium fibre mats require uniform distribution of fibres to ensure the stability and consistency of their porous structure. This process requires highly accurate fibre placement techniques:
Maintaining uniform porosity (common requirements are 50-70%).
Controlling fibre thickness and stacking density.
Solution:
Use of automated fibre lay-up equipment and precision web lay-up process with optical monitoring and adjustment techniques to ensure that the laid fibres are neatly aligned and free from faults.
- High temperature sintering process
Technical difficulties:
Sintering is the key process to form the three-dimensional mesh porous structure of titanium fibre mats, and the difficulty lies in:
Precise control of the sintering temperature (usually between 800°C and 1000°C).
Preventing over-sintering or incomplete sintering of the fibres.
Ensuring uniform pore size distribution and strong inter-fibre connections.
Solution:
Use a high precision vacuum sintering furnace combined with a computerised temperature control system and atmosphere protection (e.g. argon protection) to ensure a stable and controllable sintering process.
- Homogeneity of porous structure
Technical Difficulties:
The porosity and pore size of Titanium Fiber Felt for PEM are critical to its properties, including gas permeability, electrical conductivity and corrosion resistance. Production process is prone to:
Uneven pore size distribution.
Porosity deviation from target values.
Solution:
Use high-precision testing equipment to monitor the porosity and pore size distribution in real time, and adjust the lay-up and sintering process parameters.
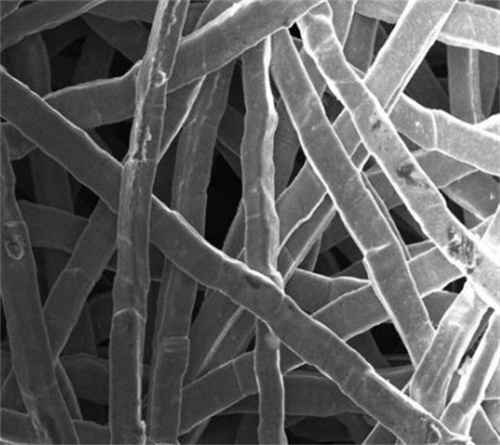
- Surface treatment process
Technical Difficulties:
Titanium Fiber Felt for PEM often requires surface treatment (e.g. precious metal coating or reactive coating) to enhance its electrochemical properties or corrosion resistance. This process requires:
Uniform coating without flaking or bubbles.
Strong bonding of the coating to the titanium substrate.
Solution:
Use of plasma spraying, electroplating or PVD (Physical Vapour Deposition) technology in combination with rigorous pre-treatment steps (e.g. cleaning and surface activation) to ensure the quality of the coating.
- Mechanical properties and dimensional accuracy
Technical Difficulties:
The strength and dimensional accuracy of Titanium Fiber Felt for PEM have a direct impact on the subsequent assembly and performance in use, which may be faced in production:
Thickness deviation.
Insufficient mechanical strength (easy to break or deform).
Solution:
Use high-precision equipment and process to control the thickness, and carry out strict mechanical property tests (such as compressive strength and tensile strength tests) for the finished products.
- Gas diffusion layer performance optimisation
Technical Challenge:
Titanium Fiber Felt for PEM is used as a gas diffusion layer (GDL), and its diffusion performance directly affects the electrolysis efficiency and fuel cell performance. Requirements include:
High gas permeability.
Stable electrical conductivity and chemical properties.
Solution:
Optimisation of gas permeability and electrical conductivity by adjusting porosity and surface coating materials.
- Corrosion resistance
Technical difficulties:
Titanium Fiber Felt for PEM needs to be used in harsh electrolytic environments and must have excellent corrosion resistance, especially to acids and alkalis and high current impact.
Solution:
Select high purity titanium fibre material and use precious metal coatings (e.g. iridium or platinum) to improve corrosion resistance.
- Consistency in mass production
Technical Difficulty:
The performance of Titanium Fiber Felt for PEM is highly dependent on production process parameters, making it difficult to ensure consistency from batch to batch in mass production.
Solution:
Adopt highly automated production lines, combined with statistical process control (SPC) methods to monitor key process parameters in real time.
- Environmental Protection and Safety
Technical Difficulty:
The production of Titanium Fiber Felt for PEM involves high temperatures, high purity gases, and chemical processing, presenting environmental and safety challenges: