PEM hydrogen production selects the perfluorosulfonic acid proton exchange membrane. It has good chemical stability, proton conductivity, and gas separation. As a solid electrolyte to replace asbestos membrane, it can effectively block electron transfer and improve electrolyzer safety. The main components of PEM water electrolyzer are proton exchange membrane, cathode catalytic layer, cathode gas diffusion layer, cathode terminal plate, etc. from inside to outside.
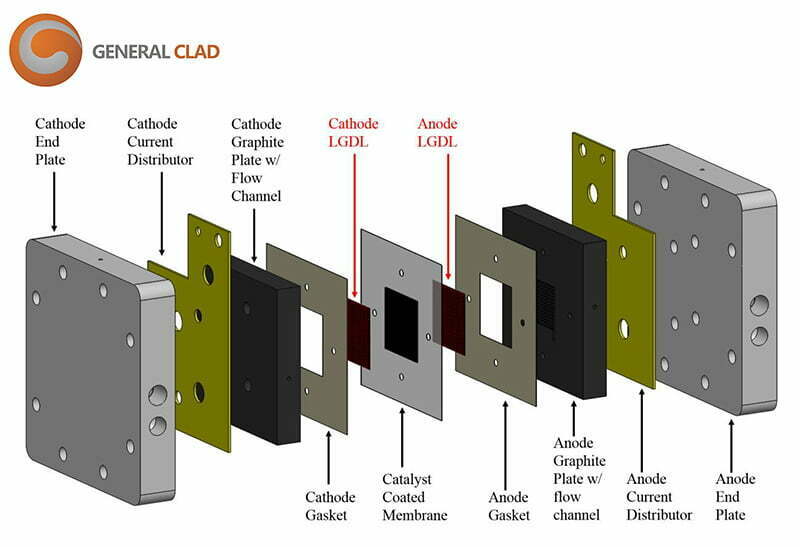
The gas diffusion layer(GDL), the catalytic layer and the proton exchange membrane form the membrane electrode. This is the main site for material transfer and electrochemical reactions throughout the water electrolyzer. Membrane electrode characteristics and structure directly affect the performance and lifetime of PEM water electrolyzer.
For GDL materials, the industry is currently using sintered felt, titanium felt and carbon felt material routes. The anode has the highest effect with titanium felt, while the cathode mainly uses carbon felt. In order to achieve the best match between the material and their own process, the diffusion layer filling material is basically required to customize. Which is also one of the core aspects that reflect the level of each process.

In addition to the diffusion layer anode filling material. The industry also uses titanium alloy materials for bipolar plates, end plates and other components. And this prevents the occurrence of hydrogen embrittlement and improves the overall safety of the equipment.