In the proton exchange membrane fuel cell, the main function of the gas diffusion layer is to support the catalyst, and to provide a channel for the gas involved in the reaction and the water produced, and it is one of the key components of the membrane electrode. The gas diffusion layer is mainly used in hydrogen fuel cells.
The gas diffusion layer is composed of a base layer and a microporous layer. Material of the base layer is mostly porous carbon paper or carbon cloth. The microporous layer is usually composed of conductive carbon black and water-repellent. In addition, the preparation method of carbon paper include: wet method and dry method. The carbon paper prepared by the wet method has a good and uniform large number of pores, and the porosity can be controlled by adjusting the amount of phenolic resin.
In hydrogen fuel cells, gas diffusion layer materials mainly include carbon fiber paper substrates, carbon cloth substrates and metal substrates according to the different substrates. Among them, carbon fiber paper has become the preferred material for commercialization due to its mature manufacturing process, stable performance, relatively low cost and suitable for reprocessing. However, with the advancement of technology, titanium fiber felt (a new material) gradually entered the market.
Parameter | Carbon fiber paper | Carbon fiber cloth | Carbon black paper | Titanium fiber felt |
Thickness(mm) | 0.2-0.3 | 0.1-1.0 | <0.5 | 0.15-0.60 |
Density(g/cm3) | 0.4-0.5 | N/A | 0.35 | N/A |
Strength(Mpa) | 16-18 | 3000 | N/A | N/A |
Resistivity(Ω.cm) | 0.02-0.10 | N/A | 0.5 | N/A |
Porosity(%) | 70-80 | 60-90 | 70 | 60-75 |
As a new material, titanium fiber felt has the following characteristics: High corrosion resistance; Three-dimensional network porous structure and High porosity; High current density and Uniform pore size distribution;
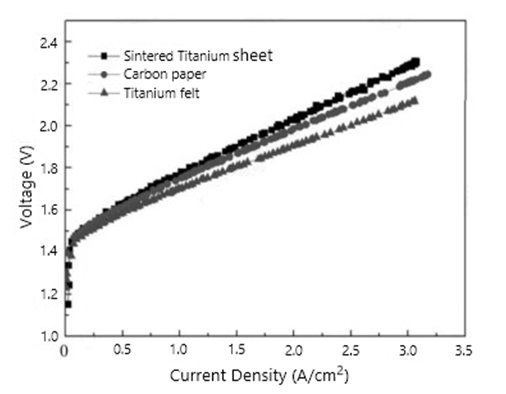
Titanium LGDL (liquid gas diffusion layer)
Electrolyzer performance with different anode LGDL thickness
Sample | Thickness(um) | Porosity |
A1(titanium LGDL) | 534 | 0.64 |
A2(titanium LGDL) | 278 | 0.64 |
A3(titanium LGDL) | 170 | 0.64 |
Figure shows the relationship between the input current densities and operating voltages needed with different thicknesses of anode titanium LGDLs with the same porosity of 0.64.
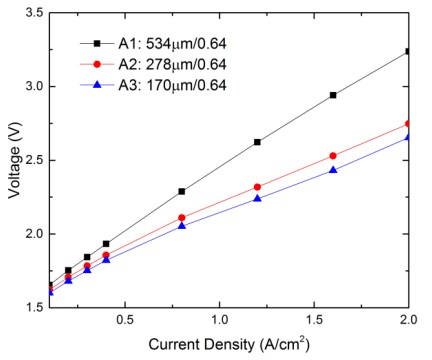
The PEMEC operated at room temperature for this testing. For all the samples, the operating voltages are increased with the input current densities, while exhibits different evolution rates. With the same current density range, a larger variation of operating voltages is obtained from the thicker LGDLs. At the same current density, the operating voltages are different from the test samples. Firstly, such as, at 1.2 A/cm2, the operating voltages are increased significantly from 2.14V to 2.62V with the anode LGDL thickness increasing from 170 μm to 534 μm, respectively. Finally, the result indicates that electrolyzer performance significantly decreased as the thickness of the LGDL increased.
Electrolyzer performance with different anode LGDL porosity
Sample | Thickness(um) | Porosity |
B1(titanium LGDL) | 204 | 0.77 |
B2(titanium LGDL) | 204 | 0.62 |
B3(titanium LGDL) | 204 | 0.27 |
With the same thickness, the effects of varying LGDL porosity was also investigated using Subgroup B. Since the LGDLs tested are titanium meshes, porosity is defined as the geometric 27 open area of the mesh.
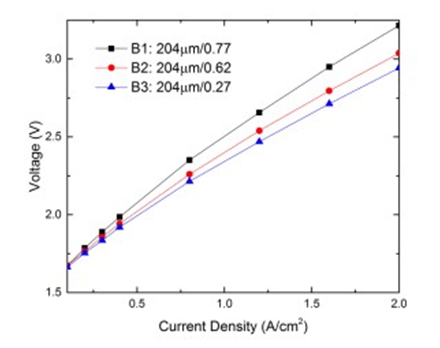
For example, for Sample B3, the LGDL has an open area of 27%, while the remaining 73% of the area was titanium. The performance results for Subgroup B are plotted in Figure 14. As the porosity is decreased from a porosity of 0.77 to 0.27 at a fixed LGDL thickness of 204 μm, the operating voltage needed is reduced at the entire current density range, which indicates a better performance. With the same thickness and same titanium fiber diameter in this subgroup, the decrease of the porosity needs to add more fibers to increase mesh numbers, thus leading to a smaller pore size. The pore sizes of the titanium LGDL samples B1-3 decreased from 699 μm, 391 μm and 108 μm, respectively.
Performance with titanium felt LGDL
Sample | Thickness(um) | Porosity |
F1(titanium felt LGDL) | 500 | 0.73 |
A1(titanium LGDL) | 534 | 0.64 |
A3(titanium LGDL) | 170 | 0.64 |
Its(F1) porosity and thickness are 0.73 and 500µm respectively, while its average pore size is about 60µm, much smaller than other titanium LGDLs. Figure shows its performance tested in the electrolyzer with a flow rate of 40 ml/min at room temperature. Similar to the other titanium LGDLs, its operating voltage is increased with current density, and it performed most similarly to sample A3. Since the felt LGDL has a smaller pore size, it can provide a better interfacial contact with the catalyst layer. Although the titanium felt LGDL is much thicker than sample A3, it still maintains a lower ohmic resistance and smaller transport resistance due to a large porosity.
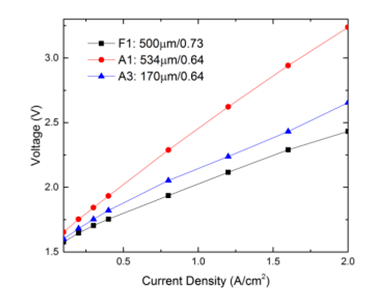
From 《OPTIMIZATION OF TITANIUM LIQUID/GAS DIFFUSION LAYERS IN PROTON EXCHANGE MEMBRANE ELECTROLYZER CELLS》
Performance requirements of gas diffusion layer:
- It exists between the bipolar plate and the catalyst layer. During the electrochemical reaction, the high current density is 2A/cm2, which has high electrical corrosion resistance and must have corrosion resistance;
- It acts as a medium for the diffusion of hydrogen/oxygen or methanol/air to the catalyst layer and must be a porous and gas-permeable material;
- Acting as a current conductor, it must be a highly conductive material;
- The reaction is an exothermic reaction. Overheating will cause damage to the proton exchange membrane. The gas diffusion layer must be made of high thermal conductivity material to conduct heat to avoid damage to the proton exchange membrane;
- The reaction of the fuel cell to produce water will cause performance degradation, so the gas diffusion layer must be able to take out the water, and the hydrophobicity must be high;
- Improve fuel cell efficiency and increase fuel cell service life.
Application:
Hydrogen fuel vehicles, military applications, commercial airliners, hydrogen-rich machines, medical, portable power supplies, etc.
Military industry:
the world’s first German U-31 submarine powered by fuel cell AIP
Aviation:
Alaka’i Technologies launched the Skai aircraft powered by hydrogen fuel cells
New energy vehicles:
Toyota’s hydrogen fuel cell vehicle Mirai officially launched in Japan on December 15, 2014